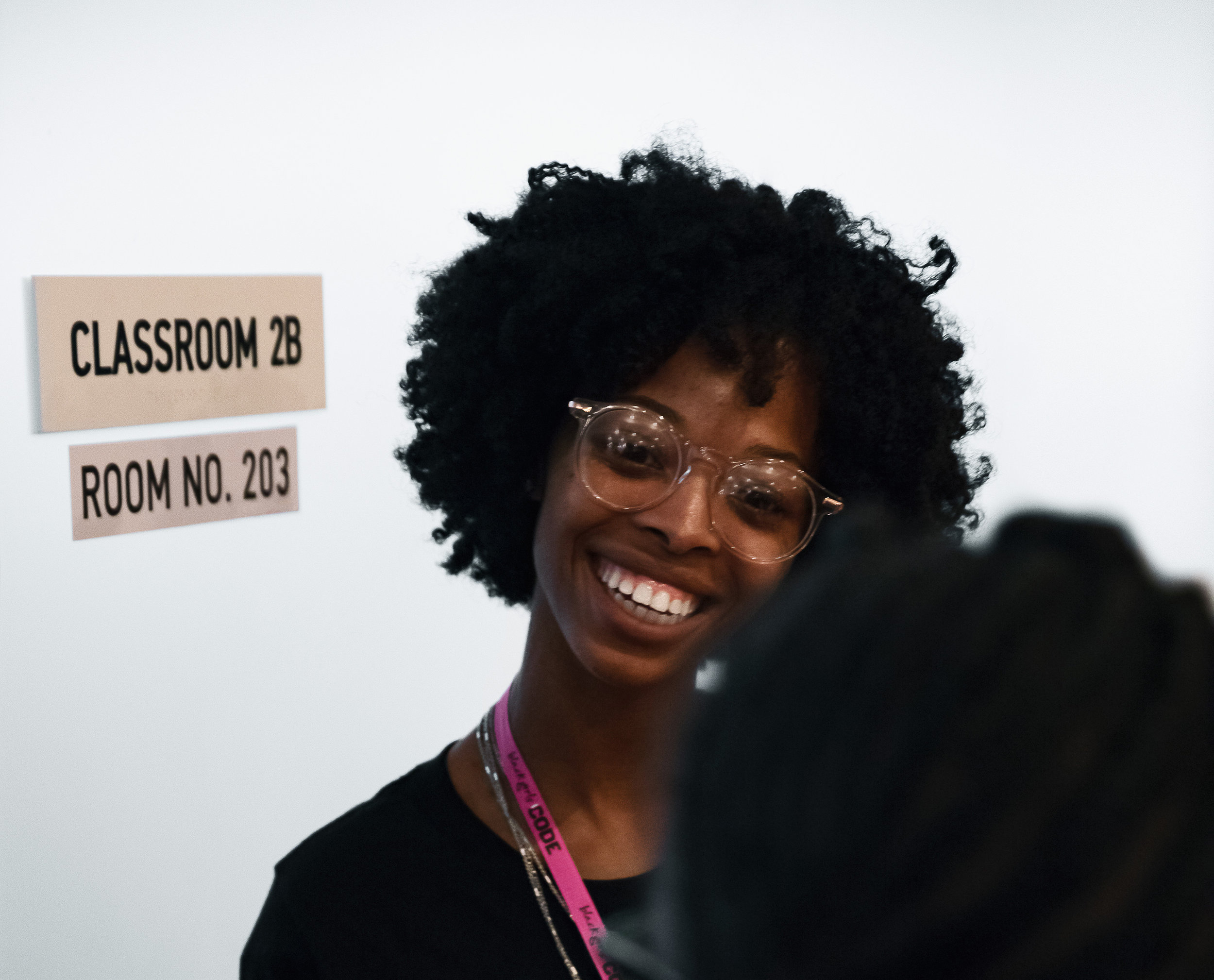
WHAT IS TRAINING WITHIN INDUSTRY
In 1940 the American Government formed many emergency services to assist in creating solutions for the manufacturing plants during World War 2. One of these emergency services was T.W.I. also known as Training Within, T.W.I. was task with discovering solutions to meet the constant demands of supplies and workforce required during World War 2.
They came up with the solution which was The Three J’s, these are T.W.I. Job Instruction (T.W.I. JI), T.W.I Job Methods (T.W.I. JM), and T.W.I. Job Relations (T.W.I. JR), they created pocket cards for each.
T.W.I. Job Instruction was about how to Instruct this entailed on how supervisors can train their workers more efficiently and improve their performance.
T.W.I Job Methods was all about improving the current method, breaking it down into details, eliminating unnecessary details, combining details when practical, rearranging details for a better sequence and simplifying the detail for an easier, safer and more reliable work method.
T.W.I Job Relations entailed on how to handle problems for when or before they occur, T.W.I. JR teaches you to gather the facts not just the numbers but the individual workers feeling and opinions. Fitting these gather facts to gather a bearing and what actions the supervisor can take that falls into the companies policies and then take action and check the results.
However Training Within Industry (T.W.I.) discovered the pocket cards weren’t enough so they created the three J programs, which were a 10 hour course that focuses on each of the individual points (improving instructing, improving current method, and handling problems as well as relations between supervisors and workers.
LEARN PRACTICAL SUPERVISOR SKILLS
Click on your favourite TWI Program to find out more:
How are TWI leadership courses taught?
TWI programmes follow a time-proven, high-impact skills training system following a clear set of core principles:
Easy to learn, but rigorous 4 step methods
Five 2 hour classroom sessions, one per day spread over one week
Developing skills, not just knowledge
Immediate real-life application
The TWI leadership programs develop problem-solving skills through repetition of simple, 4-step patterns. Each program comes with a pocket-card that keeps TWI learners on the ‘straight and narrow’ of the method. Through repeated application of the Training within Industry method, learners internalise the pattern until they master the method and it becomes second nature. Thus, when confronted with a problem, TWI practitioners automatically apply this pattern without having to think about it.
Training within Industry classes fit the busy lives of supervisors. In five streamlined two-hour training sessions over five days, supervisor learn and practise skills in leading (TWI JR), instructing (TWI JI), continuous improvement (TWI JM) and problem solving (TWI PS). Once they understand the TWI techniques and are able to apply them in their own workplace on a daily basis to improve performance and develop their teams.
TWI emphasises learning by doing. About two thirds of the 10 hours of session time is dedicated to practical demonstrations where participants apply the methods and get constructive feedback from their peers and their certified TWI trainer. Through iteration and coaching, learners discover the true meaning of the 4 step method, and fine-tune their skill in applying it.
In between sessions, participants immediately apply what they learn in their work-place. During the training week, many organisations kick off pilot projects that enable participants to solve real-life problems and demonstrate the value of the TWI skills to the rest of the organisations. This also reinforces the learning and is the first step in making TWI skills part of their daily work.
TWI Job Instruction TWI JI
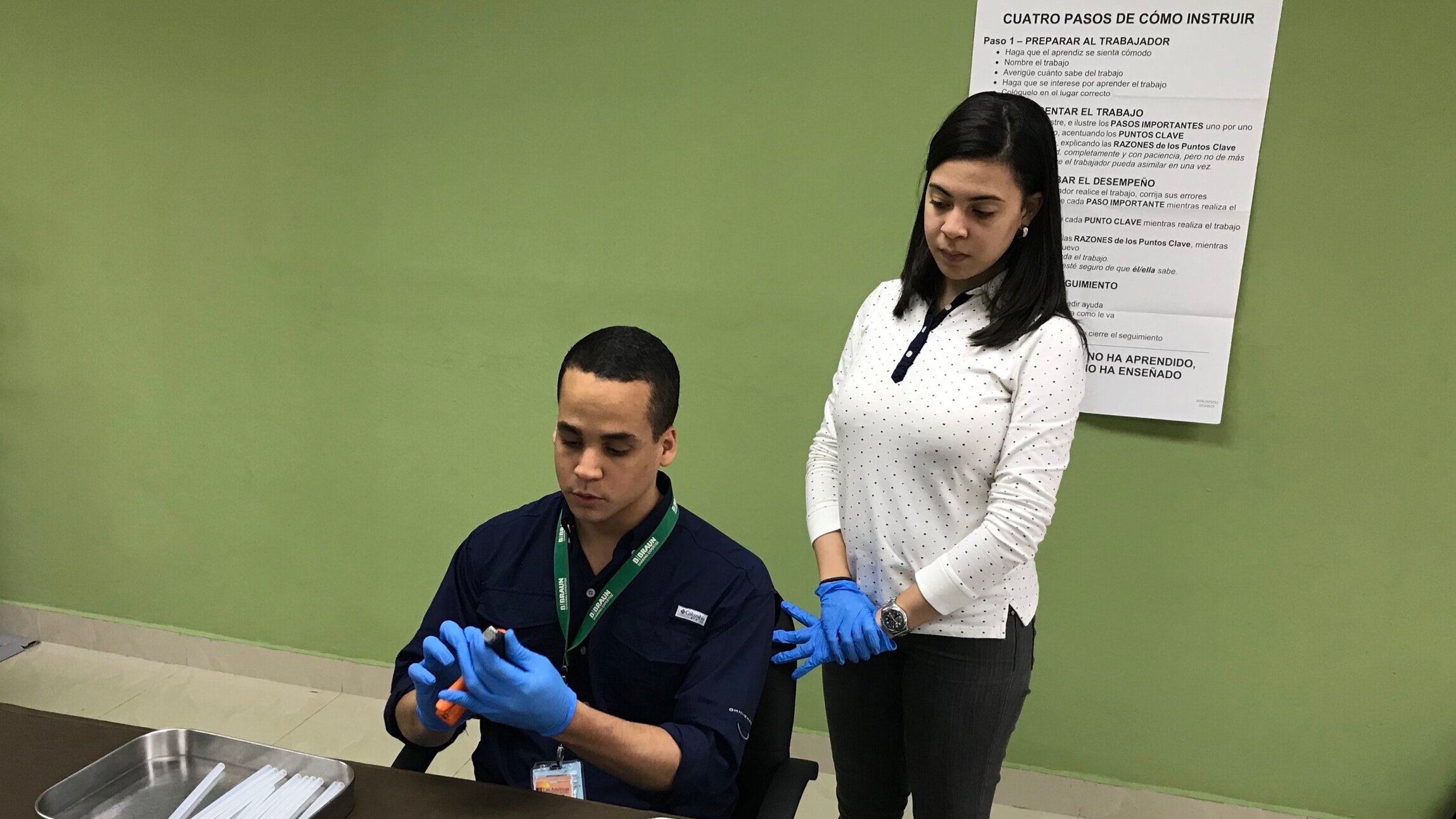
Why TWI Job Instruction?
The ability to train others is one of the most important supervisors skills. The performance of managers, value stream leaders and team leaders depends on the skills of their team. Productivity and service quality are determined by each team member’s know-how and their discipline in applying standard work.
TWI JI dramatically compresses learning-curves for new employees and those in cross-training, ensuring they achieve competence and productivity standards for a task in a fraction of the time. This allows leaders to reduce employee onboarding costs, eliminate skills bottlenecks, and increase flexibility faster. And, because on-the-job training follows a carefully scripted standard based on best-practice, organisations using TWI JI boost productivity, quality and safety, too.
TWI Job Instruction allows leaders to capture the know-how of the most experiences and best-performing workers and share it across the team, so others can apply the know-how in their work and ‘level up’. Through TWI JI, new insights and knacks gained by individuals through experience, and new methods developed through continuous improvement events or by process engineering can be passed on quickly in a way that ‘sticks’. By ensuring everyone consistently performs the work in the best way known today, supervisors are able to stabilise processes, squeeze out mistakes, boost productivity.
TWI JI lays a solid the foundation for rapid continuous improvement. TWI Job Instruction is the way standardisation is achieved and learning organisations are built from the ground up. In the Lean Manufacturing and Lean Service community, we know that ‘without standard work there cannot be improvement’. We can see this effect from experience, when the new, better method developed through Kaizen team improvement just won’t stick and performance keeps slipping back in a ‘two-steps-forward, one-step-back’ kind of way. Through TWI JI organisations get to ‘do’ standardised work in a hands-on, practical way, allowing them to collect and sustain the gains from improvement projects and events.
TWI Job Instruction - Program overview
Skill developed: on-the-job training & process standardisation
Business benefits:
compressed time to competence for new employees
rapid cross-training, eliminating skills bottlenecks and increasing flexibility faster
increased process stability, minimised mistakes and defects
boosted productivity
faster improvement through effective standardisation
reduced employee turn-over
What participants will be able to do:
capture know-how & prepare training using TWI JI breakdowns
use the TWI JI 4-Step method to train others
anticipate training needs and plan operational training
develop and install standard work in their team
Other training deliverables: 2-3 TWI Job Instruction improvement projects completed within 4-6 weeks of initial training
Training schedule: 10 hours in class + 20 hours work-place application
Participants: 7-10 participants
Training location: on-site, at the workplace
TWI Job Relations
TWI JR
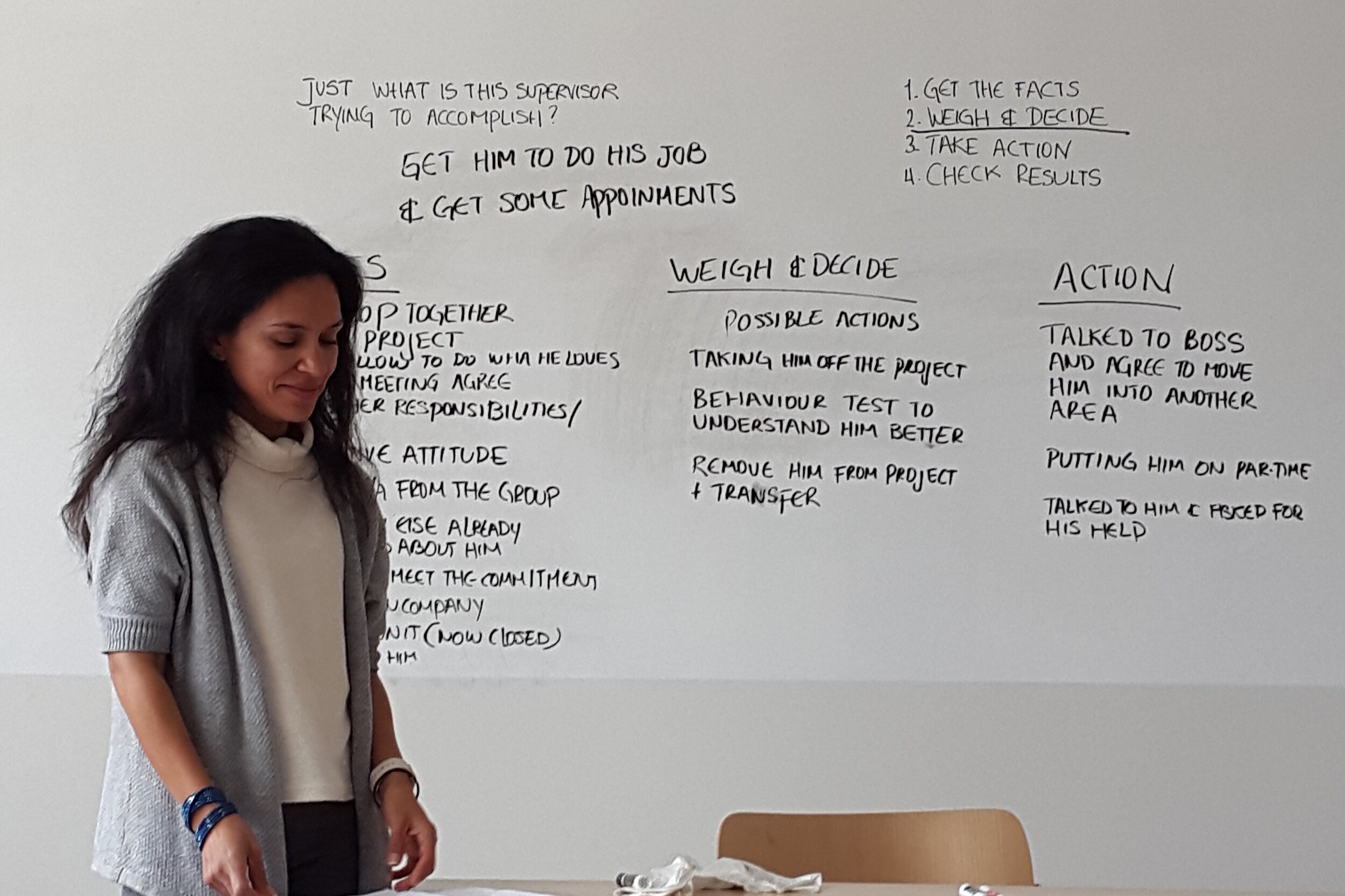
Why TWI Job Relations?
At a time of increasing competition for staff, the quality of leadership is more important than ever. Despite this, studies show that a significant proportion of employees across the world today are ‘actively disengaged’. This is reflected in reduced productivity, increased absenteeism and high employee turnover.
TWI Job Relations training gives companies an off-the-shelf solution to improve the quality of leadership of their first-line supervisors and middle-management. How they manage others is central to how the organisation is viewed by its employees, how likely they are to stay and how they perform. After all, first-line supervisors are the line managers of 50% - 75% of the entire workforce of a typical organisations.
Supervisors and managers get results through others. Their teams’ performance is directly influenced by the quality of their leadership. Supervisors and managers are leaders when their people follow them. In TWI Job Relations we say, that great supervisors get their people to do what needs to be done, when it needs to be done and in the way it needs to be done because they want to do it - not because they are told to.
TWI JR teaches supervisors this skill of leading others. They learn recognise and get into people problems early, when they are still small and easy to solve. They learn how to analyse problems with attitudes, behaviours and relationships, generate a broad range of possible actions and implement the right actions daily and at the right time for optimum results for all involved. Participants of TWI Job Relations training also learn easy routines which, when they are applied daily, greatly strengthen relationship with individuals and within the team and build strong bonds of trust that boost employee engagement, grow performance and unlock discretionary effort.
TWI Job Relations - Program overview
Skill developed: solving people problems, building trust & team-work
Business benefits:
boosted employee engagement
improved attitudes and relationship within teams
accelerated change management
enhanced team and individual performance
improved motivation and effectiveness of front-line leaders
significant reduction in employee turnover
What participants will be able to do:
Motivate teams and individuals through high-impact, daily leadership routines
Anticipate, spot and solve people problems early, before they escalate
Solve problems with attitudes, behaviour and relationships quickly, fairly and sustainably
Other training deliverables: Each participant has completes a personal TWI Job Relations project within 4-6 weeks of initial training.
Training schedule: 10 hours in class + 20 hours work-place application
Participants: 7-10 participants
Training location: on-site, at the workplace
TWI Job Methods
TWI JM
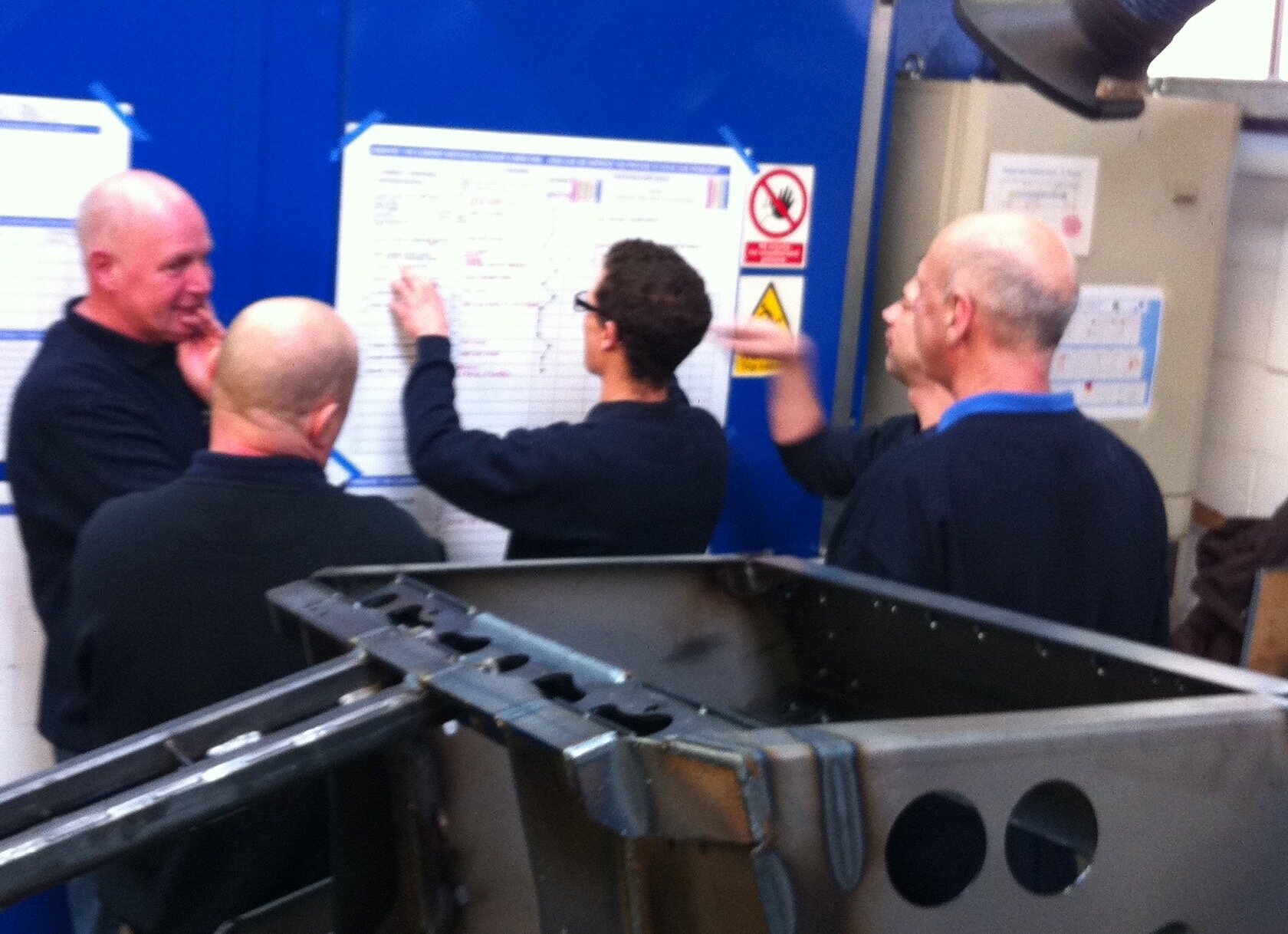
Why TWI Job Methods?
True continuous improvement happens when we engage the hearts and minds of our people, not just their hands. And when we give them a common language and technique for improving together. Many organisations struggle with this. Continuous improvement is not continuous when it remains the domain of a handful of Lean or Six Sigma experts.
Like all TWI programs, TWI Job Methods makes rigorous process engineering and leadership skills accessible to everyone in an organisation. It provides a common language for improvement and enables supervisors to generate daily, team-based improvements that are truly continuous.
Through TWI JM workers are able to simplify and improve their own processes: boost productivity, squeeze out mistakes, develop and share best practice amongst themselves. Practitioners of TWI JM prepare detailed process analyses of jobs, and then question each detail rigorously to determine anything that should be eliminated, combined, rearranged or simplified.
This disciplined Kaizen approach multiplies the number of improvement ideas generated and implemented for organisations using TWI Job Methods. TWI JM also boosts employee engagement, as workers get energised by being able to shape and improve their own workplaces.
TWI Job Methods - Program overview
Skill developed: improving processes & methods
Business benefits:
robust, simple, efficient processes
boosted productivity
significant reduction of mistakes, rework and defects
energised Kaizen activity
many more implemented improvement ideas
increased employee engagement
What participants will be able to do:
Analyse processes and methods quickly and in detail
Generate a multitude of ideas to optimise processes & methods
Prepare clear, professional proposals to sell improvements to management and peers
Rapidly test and implement improvements and evaluate their results
Other training deliverables: 2-3 TWI Job Methods pilot projects completed within 4-6 weeks of initial training
Training schedule: 10 hours in class + 20 hours work-place application
Participants: 7-10 participants
Training location: on-site, at the workplace
TWI Job Safety
TWI JS
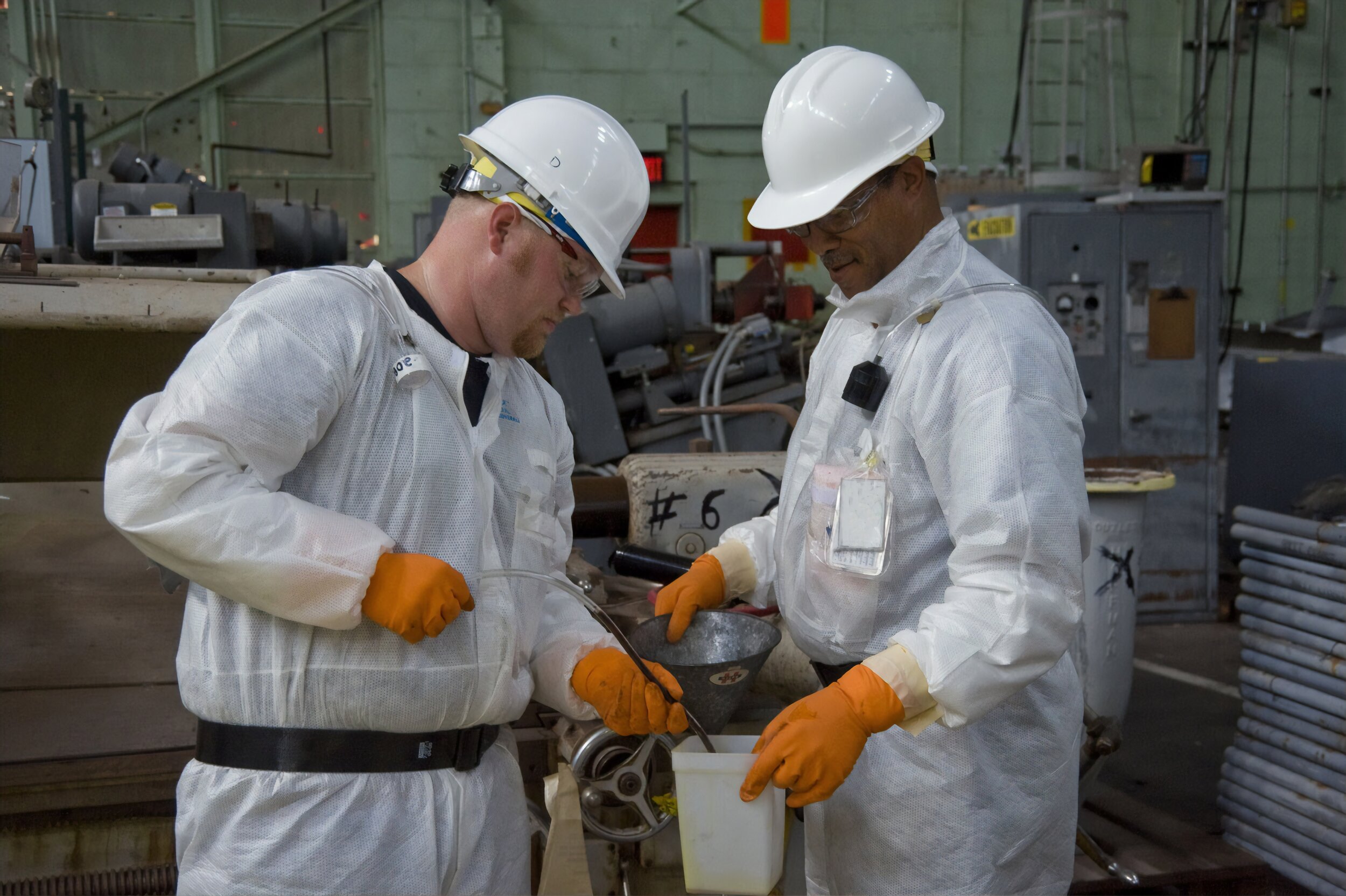
Why TWI Job Safety?
Job Safety underpins every aspect of work undertaken in an organisation. On the one hand, there are legal obligations every supervisor and manager assumes for his or her fellow workers, and serious risks of litigation to an organisation in case someone should get hurt. On the other hand, good managers and supervisors understand that the law prescribes minimum standards that can and should be bettered in a spirit of true respect for people and continuous improvement of safety. Risks and threats in the workplace and our environment are constantly evolving. The best results in safety are achieved when the majority of the people are actively engaged in, and have the means to, improve safety in their own areas.
Safety is an important aspect of all Training within Industry programs. A strong safety culture is built through the way we design our work (TWI Job Methods), the way we instruct the work (TWI Job Instruction) and the way we lead and motivate our people (TWI Job Relations). But to fully leverage these TWI skills for the benefit of Safety, supervisors and managers must develop the skill in foreseeing and preventing incidents and injuries.
This skill can be learnt through TWI Job Safety training. TWI JS teaches how to see risks holistically. Managers, supervisors and their teams learn to see how physical causes and people causes are linked together in a chain of causation that leads to incidents, accidents and injuries and, ultimately, costs. This allows supervisors to devise appropriate countermeasures early on to break this chain and, through this, protect their people, their organisation and their community.
TWI Job Safety - Program overview
Skill developed: anticipating and preventing safety risks
Business benefits:
reduction of near misses, minor and lost time injuries
reduction of long term damage and repetitive strain
active participation of workforce in risk prevention
improved employee motivation
What participants will be able to do:
Spot and foresee causes of safety incidents and injuries
Assess risk holistically, considering things, people and regulations
Generate a range of counter- and back-up measures
Implement, monitor and evaluate results
Other training deliverables: Individual TWI JS pilot projects completed within 4-6 weeks of initial training
Training schedule: 10 hours in class + 20 hours work-place application
Participants: 7-10 participants
Training location: on-site, at the workplace
TWI Problem Solving
TWI PS
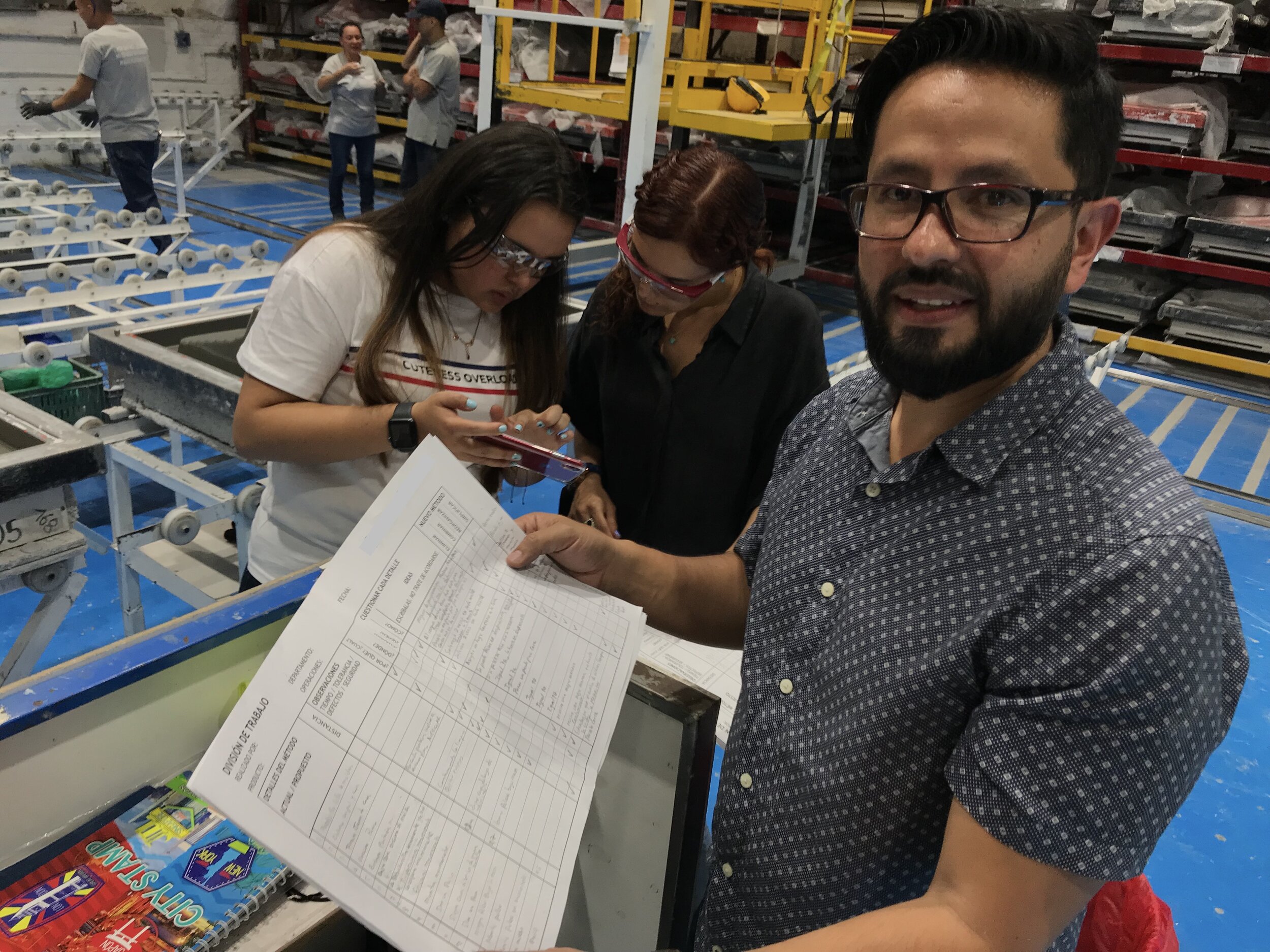
Why TWI Problem Solving?
The ability to quickly and correctly analyse and respond to problems is a hallmark of good supervisors. Unfortunately, in high-pressure operations environments, responses remain at the ‘containment’ stage of problem solving, without solid countermeasures that prevent recurrence. This leads to high-energy, time-consuming fire-fighting that ensures today’s production but does little to improve tomorrow’s performance. As a result, when problems and management pressures escalate, special projects and ‘back to basics’ initiatives are launched periodically to regain stability with huge effort, mediocre results and little hope of sustainability.
TWI Problem Solving builds the capability of supervisors to quickly identify the true causes of problems and rapidly implement sustainable countermeasures that prevent problem recurrence. In doing this, TWI PS takes a holistic view of problems - considering both process and people - whilst trying to identify the visible and hidden causes of problems, so they can be addressed. TWI Problem Solving integrates the foundational skills of TWI Job Instruction, TWI Job Relations, and TWI Job Methods into one comprehensive but easy to use method.
Companies serious about operational excellence, process stabilisation and standardised work find that TWI PS is the ideal supervisor toolkit to drive and support their efforts at the front-line. Daily application of TWI PS by team-leaders and supervisors is a highly effective way of optimising standard work and ensuring its application - thus creating stable, predictable processes that deliver reliable results every day.
TWI Problem Solving - TWI PS
Skill developed: solving complex problems involving people and process
Business benefits:
solid root-cause analysis, resolution and prevention
boosted productivity
drop in mistakes and rework
stable, predictable process performance
accelerated standardisation and improvement
What participants will be able to do:
Identify the makeup of a complex problems and isolate its main drivers
Analyse direct and indirect causes and their cause-effect relationships
Design targeted countermeasures that sustainably fix people and process problems
Monitor and evaluate impact in process and people
Other training deliverables: 2-3 TWI Problem Solving pilot projects completed within 4-6 weeks of initial training
Training schedule: 14 hours in class + 20 hours work-place application & coaching
Participants: 7-10 participants
Training location: on-site, at the workplace